Building with purpose
See my impact, ask my network
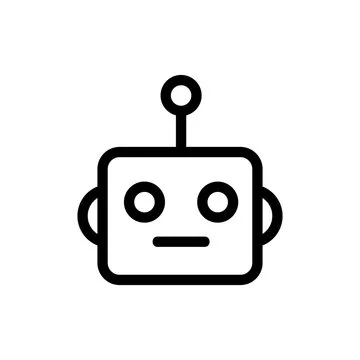
Mechanical Engineer @Stealth Robotics Startup - Jun 2025-Present - FT, Mountain View
I've joined a robotics startup currently in Stealth mode. Stay tuned for details coming soon!
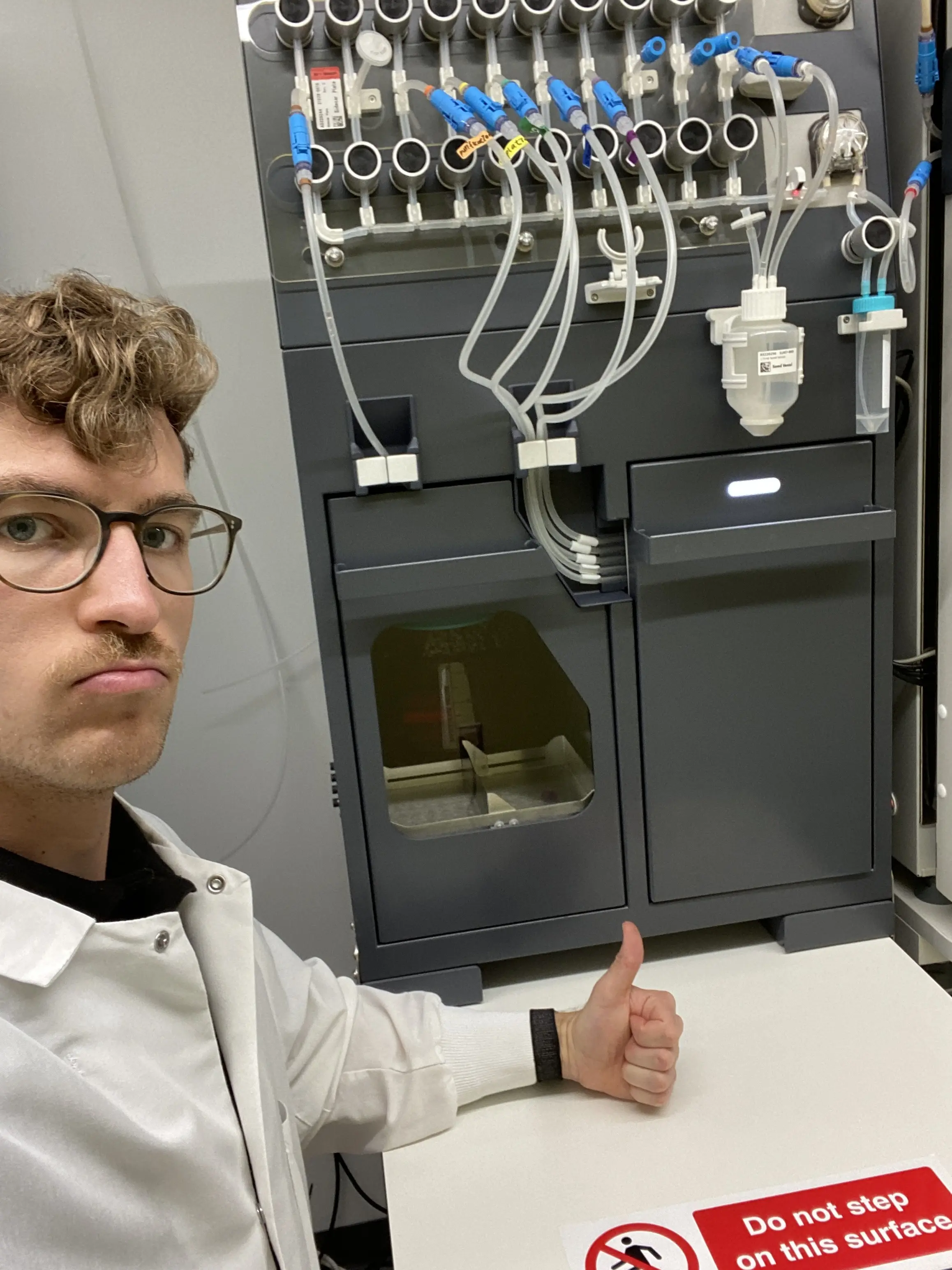
Mechanical Engineer @Mytos - Jan 2024-Nov 2024 - FT, London
B2B lab automation tech - I joined the team just as they had wrapped up design of the second generation of their cell factory platform, taking on a highly diverse role that saw me come to figure out all sorts of challenges scaling up production, getting units in the field, and driving continuous improvement. There were some very exciting new technology spaces I had to master. It was only my abrupt need to relocate back to SF with my partner that had me depart so soon. The company was actually formed in YC and had a strong "Bay Area atmosphere"
- Hardware lead for scaled-deployment & DVT of iDEM Single flagship automated cell manufacturing platform - drove progress from early production builds through first international installations & field support
- Co-led extensive firefighting efforts involving RCA, triage, and total-resolution of diverse electromechanical failures; outcomes spanning patches, formal redesigns, QI SOPs, novel tooling, and better response practices
- Designed & executed new processes for rapid scaling: SOP dev, pre-compliance/spec validation, reliability testing, DFM revs, installation/logistical procedures; compressed commissioning timelines by >60%
- Shipped novel HW features from blank sheet: vapor-H2O2 decontamination, HW UX upgrades, flat-pack structures for system stacking, anti-fungal material changes - many more fully conceptualised for later rollout
- Ideated and completed numerous SPIKES investigating potential systemic issues, new features, and hardware upgrades
- Key player in selecting, then porting over to new CAD platform (Solidworks to Onshape)
Talk to: Felix (manager), James (manager), Ignacio (Co-founder)
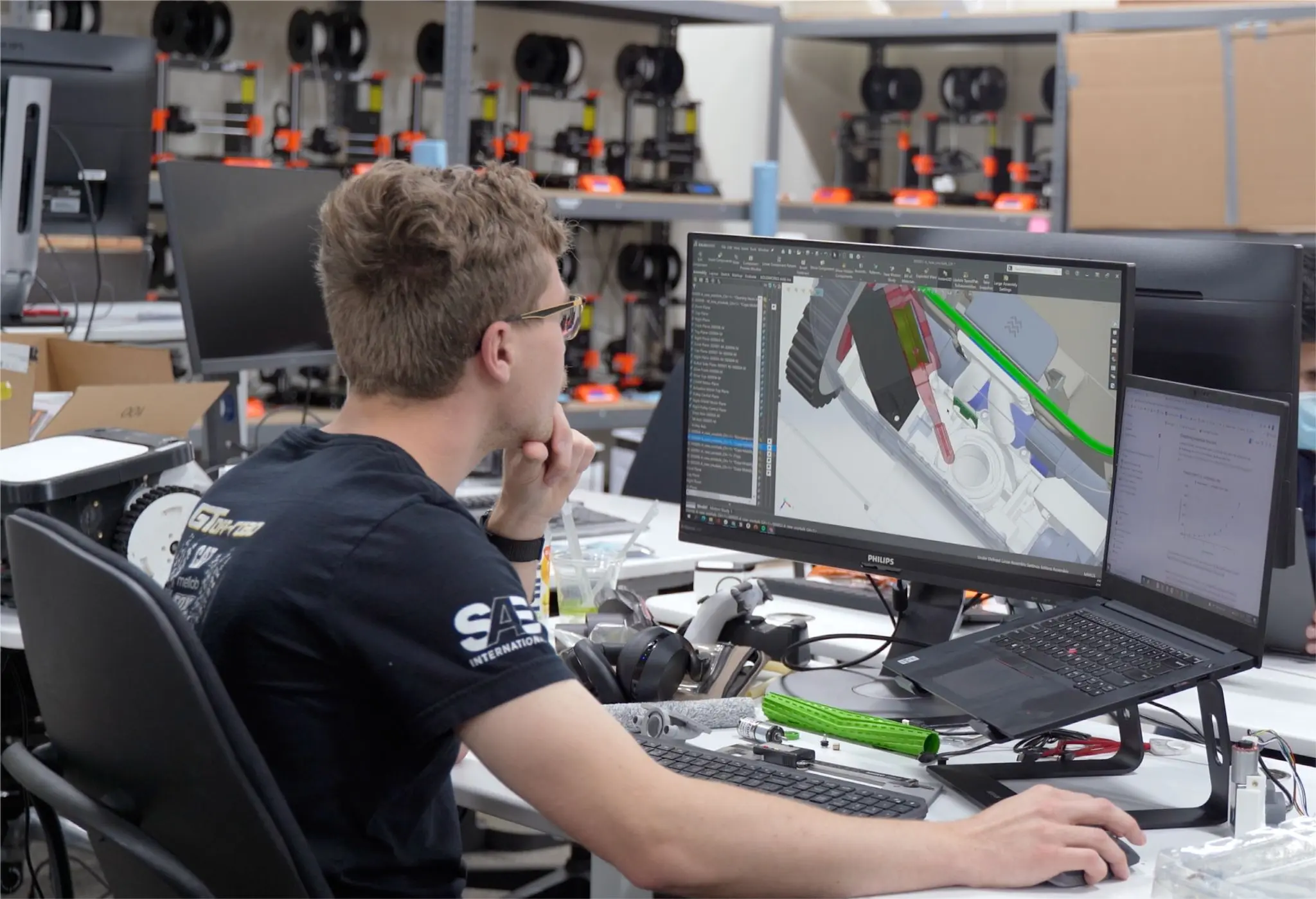
Mechanical Design Engineer @Matic - Aug 2021-July 2023 - FT, Mountain View
Consumer robotics - This role was initially prototyping/R&D oriented, with a mandate to create something original in form and function. With increasing design progress, it became more about EVT and DFM. We were producing most parts on hard tooling and shipping the first few production units by my departure.
- Sole DRI for cleaning-head subsystem for flagship autonomous CV/AI home cleaning robot; created an original architecture of hundreds of unique components, mechanisms, motorised systems, & sensors from almost blank-sheet through first high-volume production runs; mostly plastic moulded with custom mechatronics
- Extensively used 3DP/rapid prototyping & custom-designed equipment to test performance, reliability, sensors at the isolated-component to entire robot scales; significant hands-on fabrication/laboratory time
- Created MCU/DAQ instrumentation & analytics tools (MATLAB/xls) to build statistical/physics models driving cleaning efficacy, noise reduction, reliability, & OTS part selection. Many leveraged across hardware team
- Wrote & deployed Python/Rust scripts to collect sensor data, then implement complex robot behavioural features for live diagnostics & situation avoidance, some patented market firsts
- Created, released & sustained >110 externally manufactured components in collaboration with suppliers/CMs across the US & Asia; closely involved at all stages: first outreach through industrialisation/quality projects
- Collaborated daily with engineers, product, supply chain, & user testing teams to ensure system level integration, spec conformance, compliance; crafted documentation, CAD & drawings (Solidworks/PDM)
- Closely involved with engineering-adjacent processes & decision making: project management, product definition, design reviews, demos, hiring, supplier relations...typical startup-esque responsibilities
- Supervised two interns
Talk to: Anshuman (manager), Vishal (manager), Navneet (CEO)
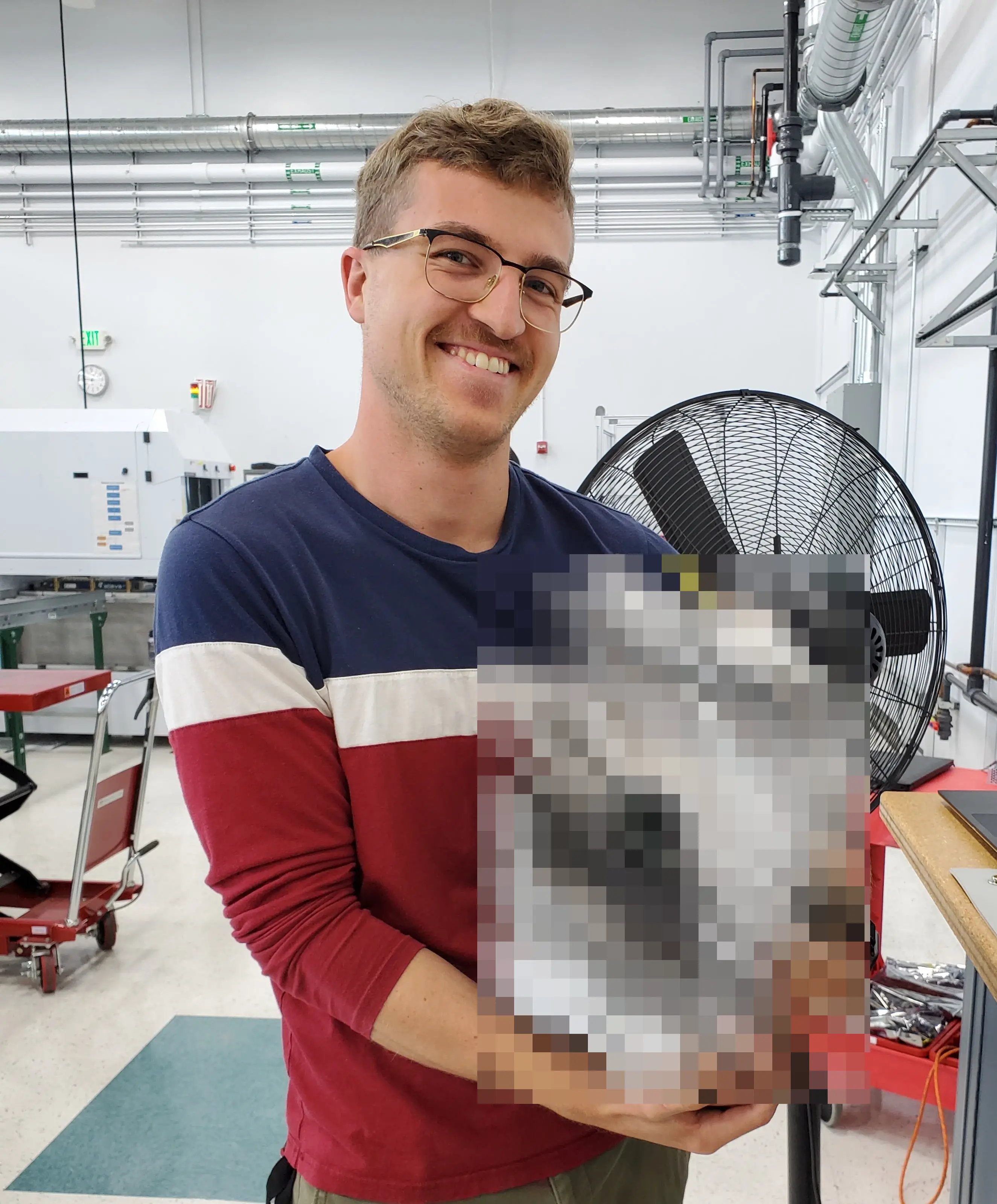
Mechanical Engineer @HV team, Lucid Motors - July 2020-Aug 2021 - FT, Newark (CA)
EVs, production/motorsports - In this highly formative role, I got exposure to the high-precision, small-scale engineering of Formula E and the colossal challenges of bringing an entire EV sedan into production for the very first time.
- Lead mechanical DRI for novel 250kW Formula E racing inverter, taken through concept, modelling, sourcing & validation, with components spanning IM plastic, formed metal, machined, PCBAs, harnesses
- Overhauled initial tendered design with material efficiency improvements & reshaping of core layout, resulting in 17% weight loss, 61% higher power density, lower part count & simpler serviceability Proactively sought out & collaborated with CMs, Tier 1s, & prototype vendors to validate DfM, continuously manage quality & handle deviations for tens of parts with volumes from 00's to 0000's
- Created virtual models for optimisations, conduct tolerance stack-ups, HV-chain safety analyses
- Wrote part/system level specifications, DFMEA reports, part/assembly drawings (CATIA) Designed assembly processes, custom jigging hardware, WIs/SOPs, & servicing routines
- Defined DV plans, physical builds/prototypes, & supported technicians through testing/rework
- Spent time on the (then burgeoning) factory floor in Arizona, troubleshooting
Talk to: Brad (manager), Rene (manager)
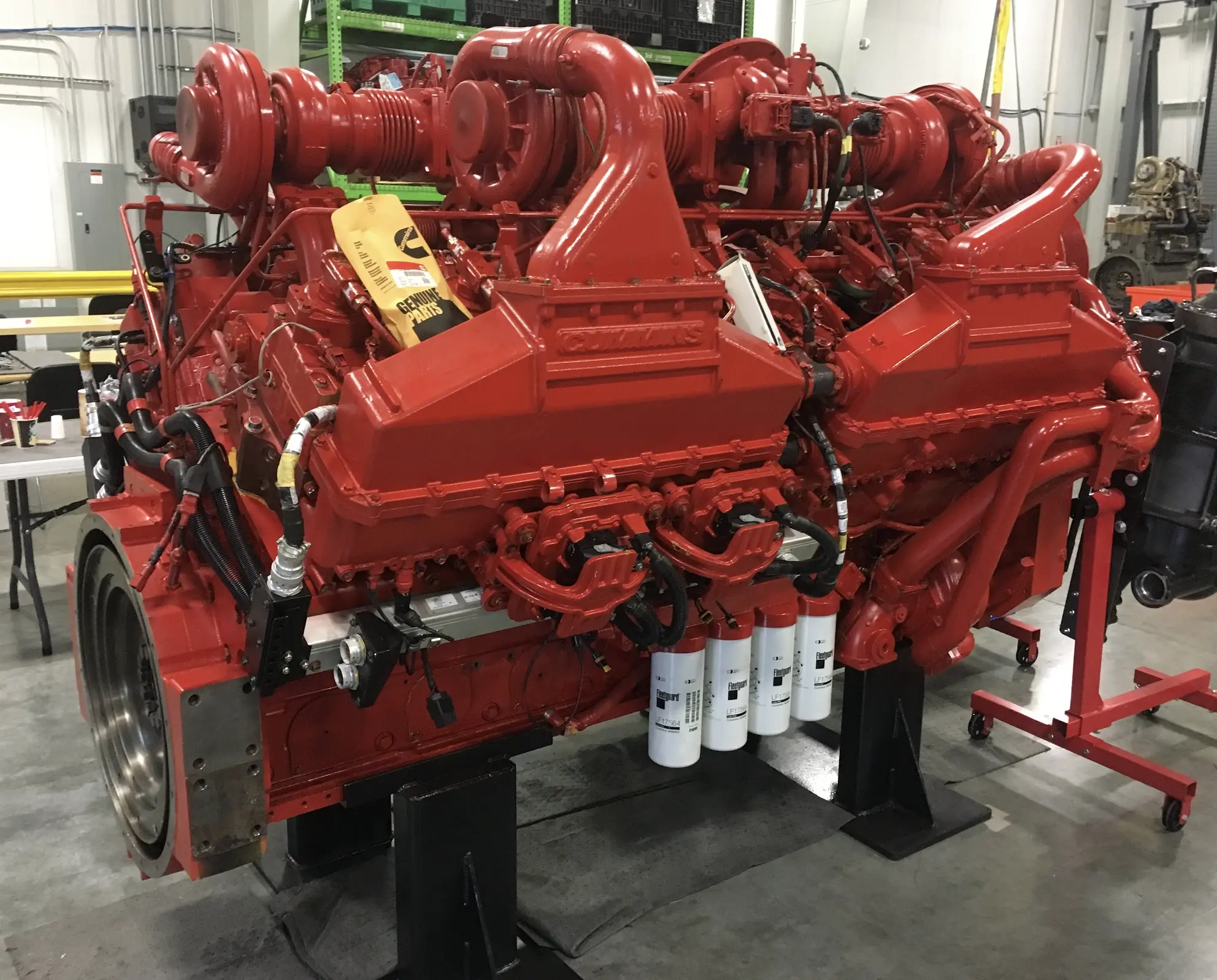
College-era experiences @Georgia Tech and elsewhere - 2016-2020
College (obviously) taught me a lot, but these extras helped me to put it all into practice at the same time, while exposing me to the pragmatic realities of engineering in the wild
- GT Off-Road - 2016-2020
- Service Engineering (III) internship @Cummins - Summer 2018
- Capstone project with Rheem Mfg Co. - Spring 2020
- Robotics design research - Summer 2019
- Stamps President's Scholarship - 2016-2020
I was all-in on the BAJA SAE racing team, where we'd design, build, and compete an off-road racing car from scratch every year. It was a hugely formative and memorable period. I ended up holding various lead positions and building out a whole new DAQ sub-team. The year I was Chief Engineer, we up-ranked from 77th to 7th place at national competition!
I interned with the top-level technical specialists in the field service engineering division of Cummins Heavy Engines in Columbus, IN. The work was modeling and performance analytics oriented, with excursions into the field all over the country.
Myself and three fellow students designed, prototyped, and subsequently won a patent for a new kind of water heater tank leak detection and shut-off device
I spent a summer within the LIDAR lab at Tech helping to design and prototype miniature actuator assemblies and MCU control infrastructure for a humanoid robot platform designed for teaching and trialling control systems.
Beyond the great privilege that was having my whole degree funded, being a part of this tight-knit leadership oriented cohort meant I got to participate in a whole lot of special curricular activities. I studied abroad in China, then again across Oceania, went to conferences, retreats, and even helped to host the SSNC19 convention. I owe this incredible bunch a great deal!